Duravit zöld A fenntartható fürdőszoba Termékciklus a Duravitnál
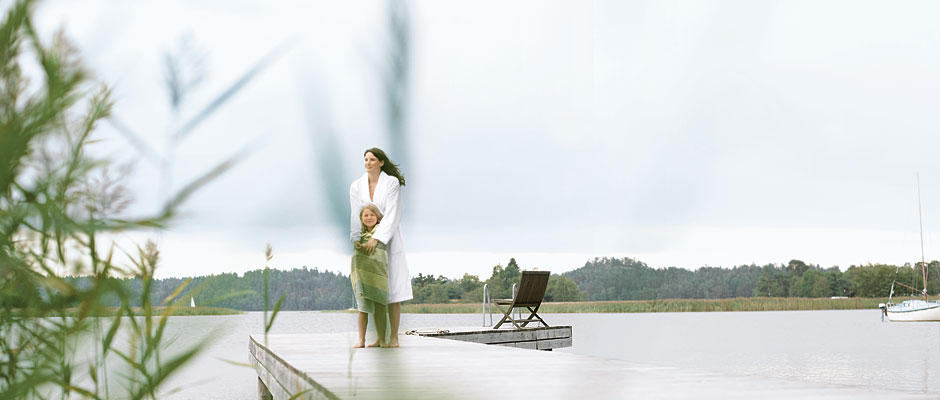
Developers and designers focus on water-saving and energy-efficient solutions, environmentally-friendly manufacture, timeless forms that retain their appeal for years and simple product assembly. In order to achieve the best possible results, Duravit enters into a dialogue with its customers, trade partners and sanitaryware dealers, as well as with retail consumers. Whether at national or international trade fairs, during seminars or in conversation with our customers, we welcome requests, ideas and criticisms, which we then analyse and process further.
Environmental compatibility of materials and resources
- The selection and purchasing of materials and components are subject to strict ecological and economical requirements.
Unconditional product safety
- Putting sanitary ceramics to the test.
At Duravit, unconditional product safety is of paramount importance. All ceramic products and bathroom furniture comply with the fundamental requirements of relevant EU directives, carry the CE mark and are subject to strict internal quality requirements that sometimes also exceed statutory standards. Numerous internal and external checks with regard to safety, hygiene, usability, noise reduction and soundproofing are carried out during product development. All products are subject to strict load tests, for example, the doors of the bathroom furniture are opened and closed 120,000 times. All bathroom furniture with electrical parts is tested for its electromagnetic compatibility (EMC) and manufactured in compliance with VDE or UL standards. Before dispatch, each individual part is subject ed to a function test.
Products are recycled
It is Duravit’s declared goal to return everything to the production cycle, wherever possible. All materials used at Duravit can be re-supplied: sanitary ceramic can be re-used in different ways. Sanitary acrylic is supplied to thermal utilization. As a rule, re-usable raw materials such as ABS plastics, board materials, fittings and glass are used for the bathroom furniture. As it is easy to dismantle, the furniture can be disposed of in accordance with the raw materials used.
Intelligent packaging management
Like the technical documentation and assembly instructions, the packaging for Duravit products consists of 60% recycled paper and can itself be fully recycled.
Like
the technical documentation and assembly instructions, the packaging for
Duravit products consists of 60% recycled paper and can itself be fully
recycled.Wherever possible, Duravit packaging is slotted together and only
glued in areas subject to particularly high loads that require additional
support. However, no other additional aids, such as metal staples, are used to
hold the packaging together. Thanks to intelligent packaging management,
pallets can be loaded with different pack sizes to avoid wasting any valuable
space during transport. When developing packaging, the intelligent arrangement
of the various elements and inserts prevents any unnecessary padding, such as
foam or polystyrene, whilst still providing maximum protection for the product
inside. In Germany and Austria, Duravit also participates in the Interseroh and
ARA redemption system.
In 2014, by actively recycling paper, cardboard, boxes, PE and PP plastics,
wood, aluminium, steel and sheet metal, Duravit was able to reduce CO2
emissions by 320 tonnes in Germany alone. In Addition 2323 tonnes of
resources werde saved.
REACH
Duravit is a manufacturer and importer of articles (products) as well as user of chemical substances. For these reasons, we pay special attention to the largest environmental laws work of the EU, the chemicals regulation REACH.
With REACH, the gaps in knowledge about the effects of using chemical substances are eliminated and thus a better protection of human health and the environment can be achieved. The issue is therefore already in the development process, with product releases, the selection of suppliers and supplier audits on the agenda. All related tasks/ responsibilities are enshrined in an internal directive.
Customer satisfaction is our top priority
Customer satisfaction is an important element that speaks volumes about the sustainability of a product. At Duravit, customer satisfaction is our top priority: as part of an internal programme with strict parameters, Duravit ensures that service data such as delivery times and supply availability are observed without any quality impairment. All technical questions are answered by Duravit employees via a dedicated Duravit hotline. Any complaints are processed quickly and competently via a uniform system that also operates at international level. Sources of error are carefully analysed in order to eliminate any production defects without delay. Surveys carried out by “markt intern”, the information service for the German sanitary industry, reflect Duravit’s good customer satisfaction record in Germany. For years, Duravit has regularly scored top marks in terms of both product quality and services.
A fenntartható fürdőszoba
Az én Pro.Duravit
Login
Feliratkozás
Regisztráljon most, hogy teljes mértékben kihasználhassa a pro.duravit oldalon elérhető összes funkciót.
Register